INDUSTRY 4.0: THE FOURTH INDUSTRIAL REVOLUTION RESHAPING MANUFACTURING
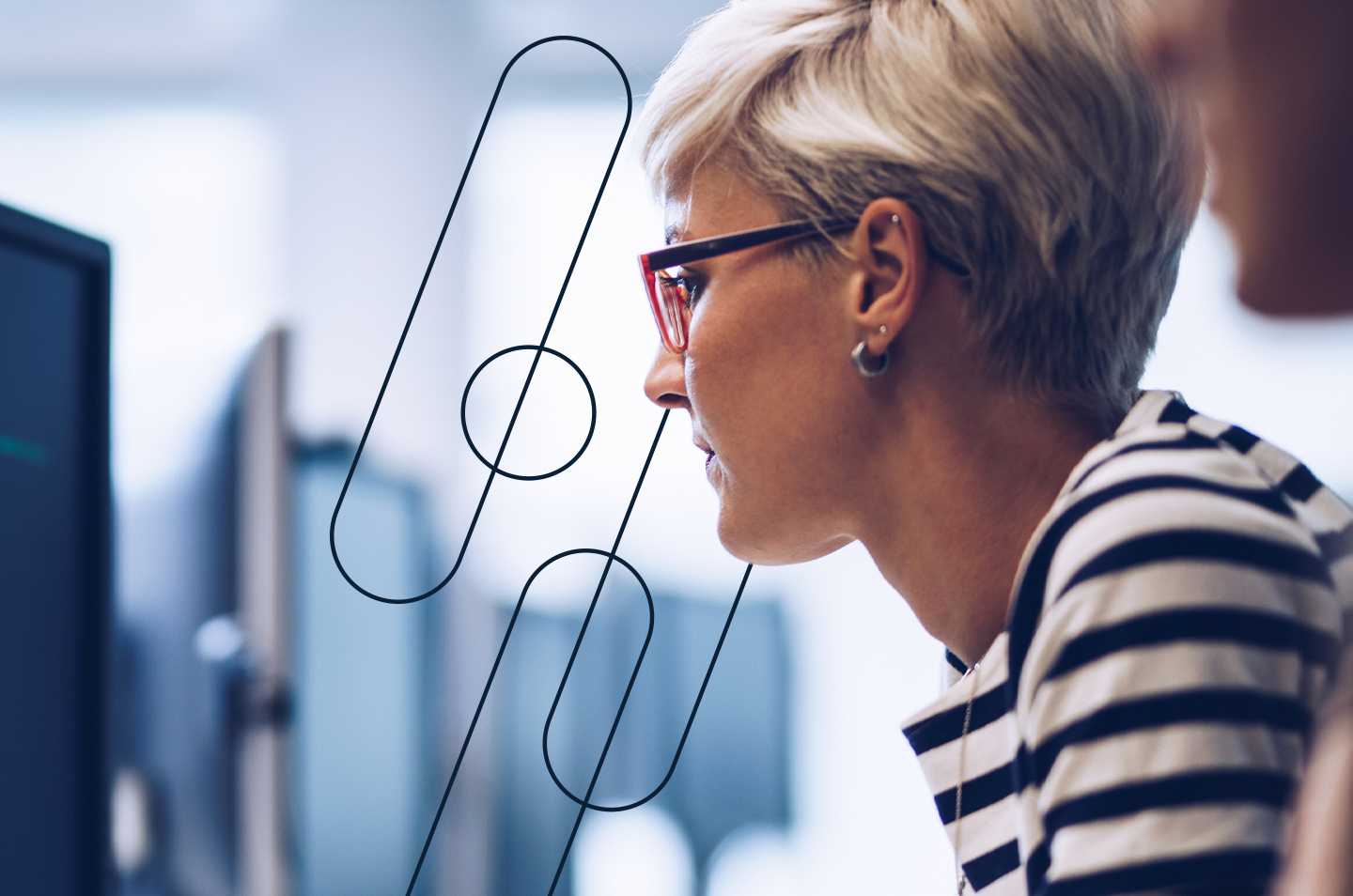
By: Shiva Mathur, Client Services Partner
The manufacturing industry is on the cusp of a revolution. Industry 4.0, also known as the fourth industrial revolution, is transforming traditional manufacturing processes through the integration of digital technologies and advanced automation. In this article, we will delve into the concepts, technologies, benefits, challenges, and future implications of Industry 4.0, providing a comprehensive understanding of this transformative phenomenon.
Redefining Business by Creating a Cognitive Ecosystem
Industry 4.0 has been at the forefront of many digital transformation discussions over the last decade. However, its traditional business intelligence model typically allowed a sequential flow of information and resources – leading to delays in actions, high customer response times, and an overall increase in cost. This can be addressed by an ecosystem-led approach that leverages key technologies and use cases to deliver integrated value, ensuring that innovation transcends industries and that insights drive the core competitive advantage.
Transformative Technologies Driving Industry 4.0
Industry 4.0 builds upon the progress made during previous industrial revolutions. It combines cyber-physical systems, the Internet of Things (IoT), big data analytics, artificial intelligence (AI), and additive manufacturing to enable a new era of interconnected, intelligent, and data-driven manufacturing.
- Cyber-Physical Systems (CPS): Cyber-physical systems combine physical components, sensors, and actuators with embedded software and connectivity. They enable real-time monitoring, control, and optimization of manufacturing operations to improve efficiency, quality, and safety. CPS facilitates the seamless integration of machines, systems, and humans.
- Internet of Things (IoT): The IoT connects devices, machines, and systems to create a vast network of interconnected entities. This connectivity enables real-time data exchange, remote monitoring, predictive maintenance, and intelligent decision-making. IoT empowers manufacturers with greater visibility, efficiency, and responsiveness.
- Big Data Analytics: Big data analytics involves the processing and analysis of large volumes of data to uncover patterns, trends, and insights. Manufacturers can leverage this data to optimize processes, predict maintenance needs, identify quality issues, and enhance product development. Real-time analytics allows for agile decision-making and continuous improvement.
- Artificial Intelligence (AI): AI technologies, including machine learning, natural language processing, and computer vision, empower machines to learn, reason, and make intelligent decisions. AI-driven applications enhance automation, predictive analytics, quality control, and demand forecasting. Intelligent robotics and autonomous systems improve productivity and efficiency while reducing human error.
- Additive Manufacturing (3D Printing): Additive manufacturing enables the creation of complex three-dimensional objects by layering materials. It offers benefits such as rapid prototyping, customization, reduced waste, and decentralized production. 3D printing revolutionizes manufacturing processes, supply chain management, and product design, opening up new possibilities for innovation.
Benefits & Opportunities of Industry 4.0
- Increased Operational Efficiency: Industry 4.0 technologies optimize production processes, reducing downtime, minimizing waste, and enhancing resource utilization. Real-time data monitoring and predictive maintenance enable proactive equipment management, ensuring optimal performance and minimal disruptions.
- Enhanced Product Quality: Real-time data analytics and AI-driven quality control systems enable manufacturers to detect defects, identify anomalies, and optimize production parameters. Advanced sensors and machine learning algorithms ensure consistent product quality, reducing rework and enhancing customer satisfaction.
- Agile & Responsive Manufacturing: Industry 4.0 enables manufacturers to respond swiftly to changing market demands.
The Next Evolution
Over the past decade since the initial launch of the Industry 4.0 framework, drivers like globalization, cost pressures, individualization, and shorter lifecycles have been working their invisible hands to shape the industry. Manufacturers around the world have been focused on achieving key outcomes around digital twins, predictive systems, near real-time visibility and connected assets by building solutions on the back of technologies like IoT platforms, AI/ML, IT/OT convergence, additive manufacturing, and more.
However, evolving market conditions have led to the emergence of new drivers, such as building disruptive business models, addressing supply chain pressure, aligning with new work realities, and, probably the most importantly, creating sustainable businesses. In addition, the technology landscape has evolved with 5G, Smart Edge, bots, extended reality, and blockchain coming into play. It is now clear that the Industry 4.0 framework needs to evolve further to address these new market realities and catch up with the capabilities of innovative technology.
AHEAD has created a transformational framework that builds upon the Industry 4.0 foundations to help our clients move towards more value-centric and purpose-driven business models. As businesses move through this journey to resilience, they will shift to ecosystem-led, integrated value delivery models driven by stakeholder collaborations at an unprecedented scale.
To learn more, contact us today.